The customers’ perception is your reality
How Unvired’s CILT Pro App Helped a Global Manufacturing Company Go Paperless for Cleaning, Inspection, Lubrication, and Tightening
A global manufacturer (packaging and recycling) deployed Unvired's CILT App to digitize their CILT (Cleaning, Inspection, Lubrication, Tightening) process, streamlining maintenance tasks and enhancing safety. The app improved equipment reliability, reduced downtime, and increased operator engagement and productivity. The app integrates with existing SAP systems and ESRI Maps, providing a streamlined process to procure materials and access locations to complete maintenance and repair tasks.
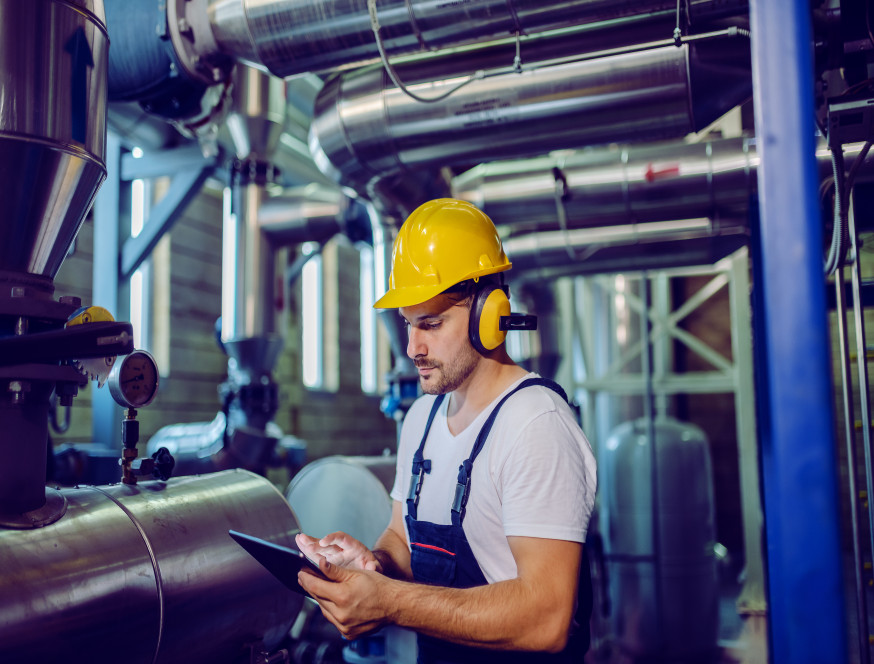
CILT Case Study for Packaging Company
Company– A Global Manufacturing Company
Industry– Manufacturing (Plastic Packaging and Recycling)
Solution– Unvired CILT Pro app to streamline the CILT (Cleaning, Inspection, Lubrication, and Tightening) Process of Autonomous Maintenance.
Business Challenges
- Manual paper-based processes for Cleaning, Inspection, Lubrication, and Tightening lead to unplanned downtime, inaccuracies, and delays in equipment maintenance.
- Limited visibility into the maintenance process results in difficulty tracking work orders and identifying potential issues.
- Unplanned downtime leads to delays and disruptions in operations, impacting productivity.
- To minimize risks, ensure compliance that equipment is properly cleaned, inspected, lubricated, and tightened as per SOPs/regulatory standards.
- Need a robust and scalable solution for maintaining a large number of pieces of equipment across multiple locations.
Solution
Deployed the Unvired CILT Pro app to streamline the autonomous maintenance processes:
- Enables operators and maintenance teams to perform their tasks effectively and efficiently through mobile devices.
- Features include task organization, task completion, maintenance history tracking, and reporting.
- Task organization helps operators and maintenance teams stay organized and ensures that each task is completed correctly and on schedule.
- Task completion allows users to digitally review task details, perform their job, and submit the task as completed.
- The app fetches all work orders assigned from the SAP Plant Maintenance/CMMS system and displays them in different tabs based on the date of execution or priority.
- The app allows users to digitally review task details, perform their job, and submit the task as completed.
- The app integrates with existing SAP systems and ESRI Maps, providing a streamlined process to procure the materials required and access the location to complete maintenance and repair tasks.
- Maintenance history tracking helps identify improvement areas and reduces the need for costly repairs and maintenance.
Benefits
- Improved equipment reliability
- Reduced downtime
- Ensured each step of CILT process was performed correctly and on schedule
- Reduced maintenance costs
- Increased operator ownership and responsibility
- Increased operator engagement and productivity
- Easy-to-use reporting and tracking maintenance issues.
About Customer
A Global packaging solutions provider that specializes in the design, manufacturing, and recycling of plastic containers.